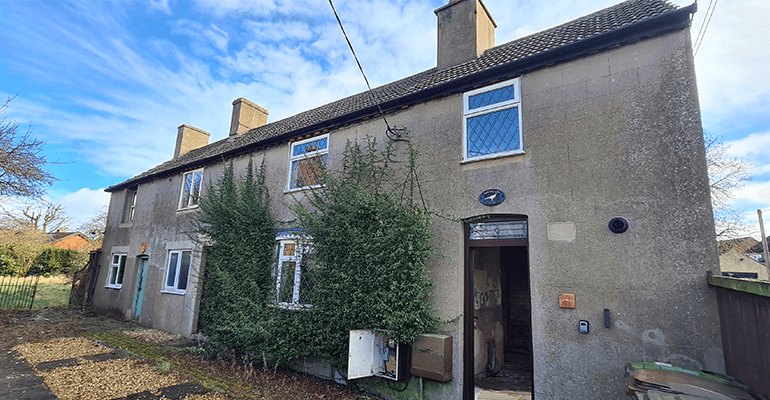
The Inside Story: A Property Investment.
If you enjoy this blog, why not check out the rest of the series?
First Blog
Diary of a Property EntrepreneurIn this exclusive diary, Saif and Kas reveal the highs and lows of an SDGB Properties renovation project that ran from December 2019 to August 2021.
December 2019
Saif Derzi
“We’ve finally got the keys for one of our upcoming projects in Lincoln. This plot came onto the market in October 2019. It’s essentially two derelict cottages, both of which are completely uninhabitable as they stand. “Because of this, we managed to secure the pair under its asking price, as there’s limited competition even from other investors at the minute. “Brexit is causing a couple of concerns currently, especially around the Price and availability of materials. But we’ve done our numbers, we’ve got the backing from Together, and we’re confident this’ll make a great family home!”
January 2020
Kas Derzi
“It’s been a couple of weeks since we got our hands on the property. As Project Manager, I usually get involved after Saif has secured the deal and set his budget. “We’d originally planned to keep the buildings as two separate properties. But after having several conversations with estate agents in the area, we’ve decided to rework the floorplan and we’re going to knock the two cottages together. “There’s a lot of demand for open-plan living and outdoor space, and the property is in a great neighbourhood – there’s a lovely school and a park on the same road. So we’re excited to create a large home for a family to enjoy!”
Saif Derzi
“When working on projects like this, we’re frequently asked why we don’t just knock everything down and start again.
“For one, it often depends on what you’ve got planning permission for – and we didn’t have the council’s permission to demolish these buildings. But we wouldn't have chosen to do so anyway, due to material shortages and price increases. In keeping the shell of the property, we’ll be saving a hefty amount on bricks and labour.”
"Here’s the existing layout and the proposed floorplan, side by side. So, as you can see, lots to be getting on with!"
February 2020
Kas Derzi
“We’re back – and this time we’ve got our team along with us. We haven’t actually touched the property yet. At this stage, I invite contractors and subcontractors to the site so they can price up properly and give us a full quote for the work. “I’ll also be making sure we’re setting clear expectations for how we’ll communicate, control quality, and just generally how we’ll keep each other updated throughout the project. “At the same time, I’m also arranging for an architect and a structural engineer to come on site and get plans drawn up. So once that’s all signed off by building control, we can get things underway. For a project of this size, this whole process usually takes about a month.”
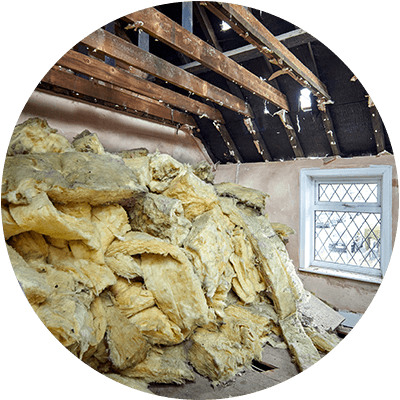
March 2020
Kas Derzi
“Once the boring stuff is out of the way, we then start the rip-out. And that means exactly that: we’re going into the property and removing absolutely everything. This has included the kitchens – well, it was just a sink and a cupboard in one of the properties – demolishing the outdoor toilet, and stripping out all wiring and plumbing.
“The property has actually been vacant for a really long time, so it’s in really poor condition.
“While we’ve got our skips, we’ll also be knocking down the walls and removing the chimney breasts to make the buildings work as one house – and to create that all-important open plan space. We’ve used a record 32 skips to clear everything!”
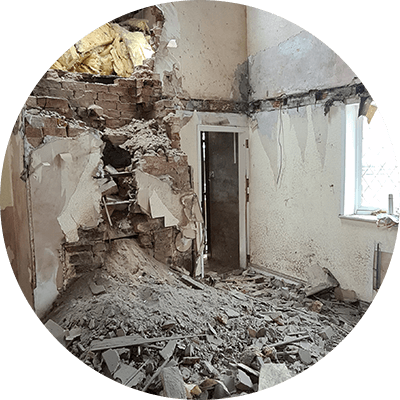
August 2020
Kas Derzi
“We’ve had a couple of delays with the onset of the Coronavirus pandemic, but we’re back on site now and raring to go.
“We’ve completed the ground works and we’ll be upgrading the floor. When we purchased the properties, the floor was all different levels so we’ve basically had to start from scratch.
“We’ve actually found it really difficult to source cement, though. It’s all being used for the HS2 rails from Doncaster to London, so sourcing and pricing has been a problem even before Covid-19.
“Luckily, we’ve found a local company who can provide us with 24 tonnes of concrete instead, which we can pour across the whole house. That’s going to save us a lot of money in labour and materials, which is always great when you’re working on a tight budget.”
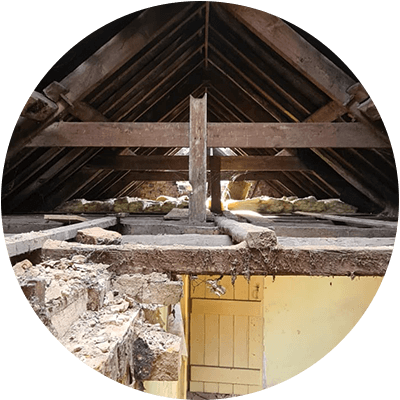
March 2021
Kas Derzi
“We’ve finished most of the really messy work now, so it’s time to start working on the outside of the building to bring its energy efficiency value up to regulation standards. When we’re insulating the property, it’s basically like wrapping a huge blanket around the entire thing.
“After we’ve had building control do the inspections to make sure it passes all of their checks, we’ll render the property to give it a great modern look.
“While all this is going on, we’re also cracking on with the electrics and re-wiring inside the property, and all of the plumbing and pipework too.”
“Plastering and boarding were next. There were exposed bricks everywhere. We’ve used plasterboard and done the skimming, alongside all the pipework for radiators, toilet, sink and so on.
“We’ve redone the layout to do the four bedrooms, bathroom and ensuite. We added a proper entrance, lobby and dining room and open-plan kitchen. In came the joiners and we did the first-fix joinery, which is putting the timber in for the wall frames. This was needed because it’s an old house. We needed to redo the stairs as the staircase is so small. Our new owners would struggle with getting furniture up! We’ve had to custom build with a degree elbow and curve to maximise property space.
“We needed to redo the stairs as the staircase is so small. Our new owners would struggle with getting furniture up!”
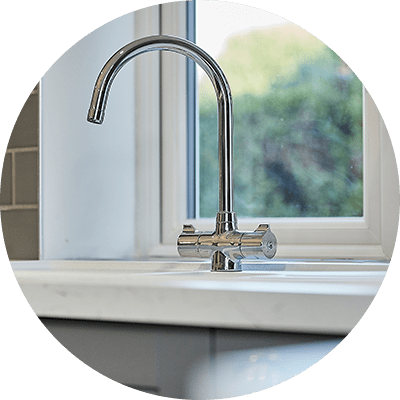
April 2021
“After that comes the second-fix joinery: hanging up all the doors and frames, architraves and skirting. Once we’ve finished these, we start fitting the kitchen and tiling bathrooms. We’re fitting baths, showers, and toilets – connecting and testing, pressure testing, flow testing, volume testing. I do all of this on site.
“We’re spray-painting the house as it cuts down the time by half. Our first coat helps us identify irregularities on the wall. We use ice lights that show any bumps or screws hanging out. We’ll then go over these again with sanding and plaster. Colour-wise, we go with white so that people can paint their new home how they prefer.
“We’ll keep a couple of tins of paint back for later on, too, as we have carpenters coming in and floorers, who will inevitably scratch painted surfaces. Landscaping-wise, we’ve got a patch of grass at the back and some paving stones going down. We have our own custom template for finding snags that we use for every refurb. This covers everything from the roof to the floors – it’s a huge list!"
June 2021
“The most exciting stage of a project for me is definitely seeing everything come together at the end. What we do is so tangible, and being able to see and touch something that you’ve created is pretty special – especially when that creation is going to be somebody’s dream home. It makes all the hard work feel worth it!”
Any property, including your home, may be repossessed if you do not keep up repayments on your mortgage.
All lending decisions are based on lending criteria and, where applicable, subject to credit check and an assessment of individual circumstances.
All mortgages are subject to our terms and conditions.
Loans offered by Together Commercial Finance Limited are not regulated by the Financial Conduct Authority.
Articles on our website are designed to be useful for our customers, and potential customers. A variety of different topics are covered, touching on legal, taxation, financial, and practical issues. However, we offer no warranty or assurance that the content is accurate in all respects, and you should not therefore act in reliance on any of the information presented here. We would always recommend that you consult with qualified professionals with specific knowledge of your circumstances before proceeding (for example: a solicitor, surveyor or accountant, as the case may be).